As homes become more sophisticated and inclusive, the role of home elevators has expanded beyond luxury to become a key element of modern residential design. The journey of a home elevator from concept to installation involves a detailed manufacturing process, characterized by precision, innovation, and craftsmanship. This article offers an inside look at what goes on in a home elevator factory, shedding light on the processes that bring these essential residential features to life.
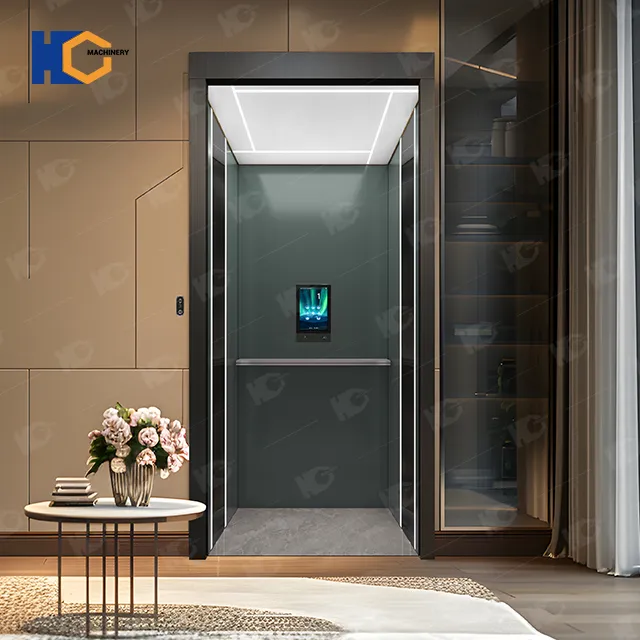
The Manufacturing Process: From Idea to Installation
- Design and Engineering
- Concept and Customization: The manufacturing process begins with the design phase, where engineers and designers collaborate to create elevators tailored to specific residential needs. Whether for a small apartment or a large mansion, the design is customized to fit the home’s aesthetics and functional requirements. Clients can choose from various materials, finishes, and configurations to personalize their elevator.
- Engineering Specifications: Detailed engineering plans are created to ensure the elevator meets safety and performance standards. This involves calculations for weight capacity, integration of safety features, and ensuring the elevator’s compatibility with the existing structure of the home.
- Material Selection and Procurement
- Premium Materials: The choice of materials is crucial for both the durability and appearance of the elevator. Factories use high-quality materials like stainless steel, tempered glass, and aluminum to produce elevators that are both robust and stylish.
- Sustainability: Many factories prioritize sustainability by selecting eco-friendly materials and adopting manufacturing processes that minimize waste and reduce environmental impact.
- Manufacturing and Assembly
- Component Fabrication: In the factory, various elevator components are fabricated with precision. This includes the cabin, doors, control panels, and mechanical systems. Advanced machinery and skilled craftsmanship ensure that each component meets exact specifications.
- Assembly Process: The assembly process combines automated technology with manual labor. Each part is carefully assembled to ensure smooth operation and safety. Quality control checks are integrated throughout the process to maintain high standards.
- Quality Control and Testing
- Rigorous Testing: Comprehensive testing is a critical part of the manufacturing process. Each elevator undergoes load tests, emergency simulations, and inspections of mechanical and electrical systems to ensure it operates safely and effectively.
- Regulatory Compliance: Factories must comply with stringent national and international safety regulations. This includes certification for safety features such as emergency brakes, backup power systems, and other fail-safe mechanisms.
- Final Customization and Finishing
- Personalized Touches: After passing quality control, the elevator is customized to include final touches such as bespoke cabin interiors, specialized lighting, and advanced control systems. This step ensures that the elevator not only functions well but also meets the homeowner’s aesthetic preferences.
- Final Inspection: A thorough final inspection confirms that the elevator is ready for delivery. This includes checking both functionality and appearance to ensure the product meets all specifications.
- Packaging and Shipping
- Secure Packaging: To prevent damage during transport, the elevator is carefully packaged. This includes securing all components and ensuring that they are protected from potential damage.
- Global Distribution: Many factories serve international markets, requiring efficient logistics to deliver elevators worldwide. Elevators are often shipped in parts and assembled on-site by experienced technicians.
Innovations in Home Elevator Manufacturing
- Smart Technology Integration
- Advanced Features: Modern home elevators often incorporate smart technology, including touchscreens, voice controls, and remote monitoring systems. These features enhance convenience and allow homeowners to control their elevator with ease.
- Energy Efficiency: Innovations such as regenerative drives and LED lighting help reduce energy consumption and lower operational costs, making home elevators more environmentally friendly.
- Modular and Adaptable Designs
- Flexible Configurations: Modular elevator systems are designed to be adaptable, allowing for customization to fit various home layouts and architectural styles. This flexibility makes it easier to integrate elevators into different residential settings.
- Luxury Options: For high-end clients, factories offer luxury features like custom wood paneling, panoramic glass, and integrated entertainment systems, adding a touch of elegance and sophistication to the elevator experience.
- Commitment to Safety and Compliance
- Cutting-Edge Safety Features: Factories continuously update their safety technologies, including advanced braking systems and emergency power backups, to ensure that elevators operate safely under all conditions.
- International Standards: To cater to a global market, factories adhere to international safety standards and certifications, ensuring that their products are reliable and compliant with safety regulations worldwide.
Conclusion: The Art and Science of Home Elevator Manufacturing
A home elevator factory is a nexus of technology, design, and craftsmanship, where every detail is carefully managed to produce elevators that enhance modern living. From the initial design and material selection to final inspection and delivery, each step in the manufacturing process is aimed at creating elevators that are not only functional but also stylish and tailored to individual needs. As the demand for home elevators continues to grow, these factories remain at the forefront of innovation, delivering solutions that combine safety, efficiency, and luxury.